|
本节内容:现代造船模式回顾,工法设计流程优化,CAE仿真分析流程(吊装和运输)。
目前,国内外各大船厂普遍采用现代造船模式。(现代造船模式,就是以统筹优化理论为指导,应用成组技术原理,以中间产品为导向,按区域组织生产,壳(船体和上层建筑)、舾(装)、涂(装)作业在空间上分道、时间上有序,实现设计、生产、管理一体化,均衡、连续地总装造船。
- 中间产品。是最终产品的组成部分。舾装单元和舾装模块是典型的中间产品。
- 分道建造。以各类分类成组的中间产品为导向,组成若干个相对独立、最大限度平行作业的生产单元,按工期要求,保持一定的生产节拍作业。
- 壳舾涂一体化作业。确立了以“船体为基础、舾装为中心、涂装为重点”的管理思想,从设计、采购、生产计划与控制等方面围绕中间产品进行协调与配合。)——以上来自百度
大型船舶船体结构的基本建造流程:零件 —— 组立(分段)—— 总段 —— 搭载;其中零件、组立、总段等均为典型的中间产品。工法设计工作的重要一环就是要保障中间产品高效率低成本的安全建造和流转(又好又快又安全——高质量)。
工法设计中存在两个主要计算场景:吊装方案设计和运输、搁置方案设计。
传统工法设计中,由于仿真能力欠缺和仿真成本较高,基本依靠“老法师”根据以往经验(踩的坑多了)进行设计,很少进行科学计算。可能导致船体结构应力集中、变形过大,影响船体建造精度且存在一定的安全风险。
典型案例:
- 搭载阶段甲板鼓起,暴力敲打或者火攻解决?
- 变形太大,影响装配精度。
- 加强太多啦,干的烦死了,能不能少点?
现在工法设计中,在方案设计阶段融入仿真分析,对方案迭代设计,优选最佳方案。但是,计算是有成本的,不要追求完美,建议事先进行筛选和排序。
CAE仿真分析流程,见附图。
需要注意的是仿真是对物理世界的抽象模拟,对模型、边界条件等做了很多简化处理,计算结果和实际会有差异。实践是检验真理的唯一标准。
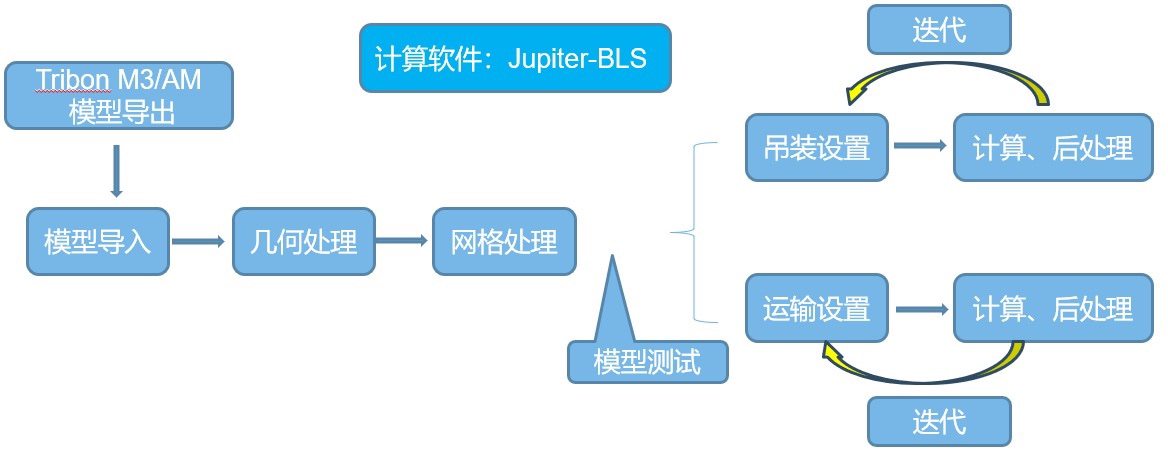
|
|